Preventing catenary rupture
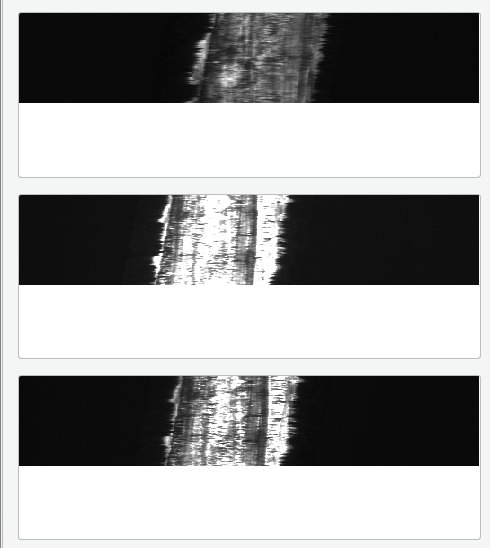
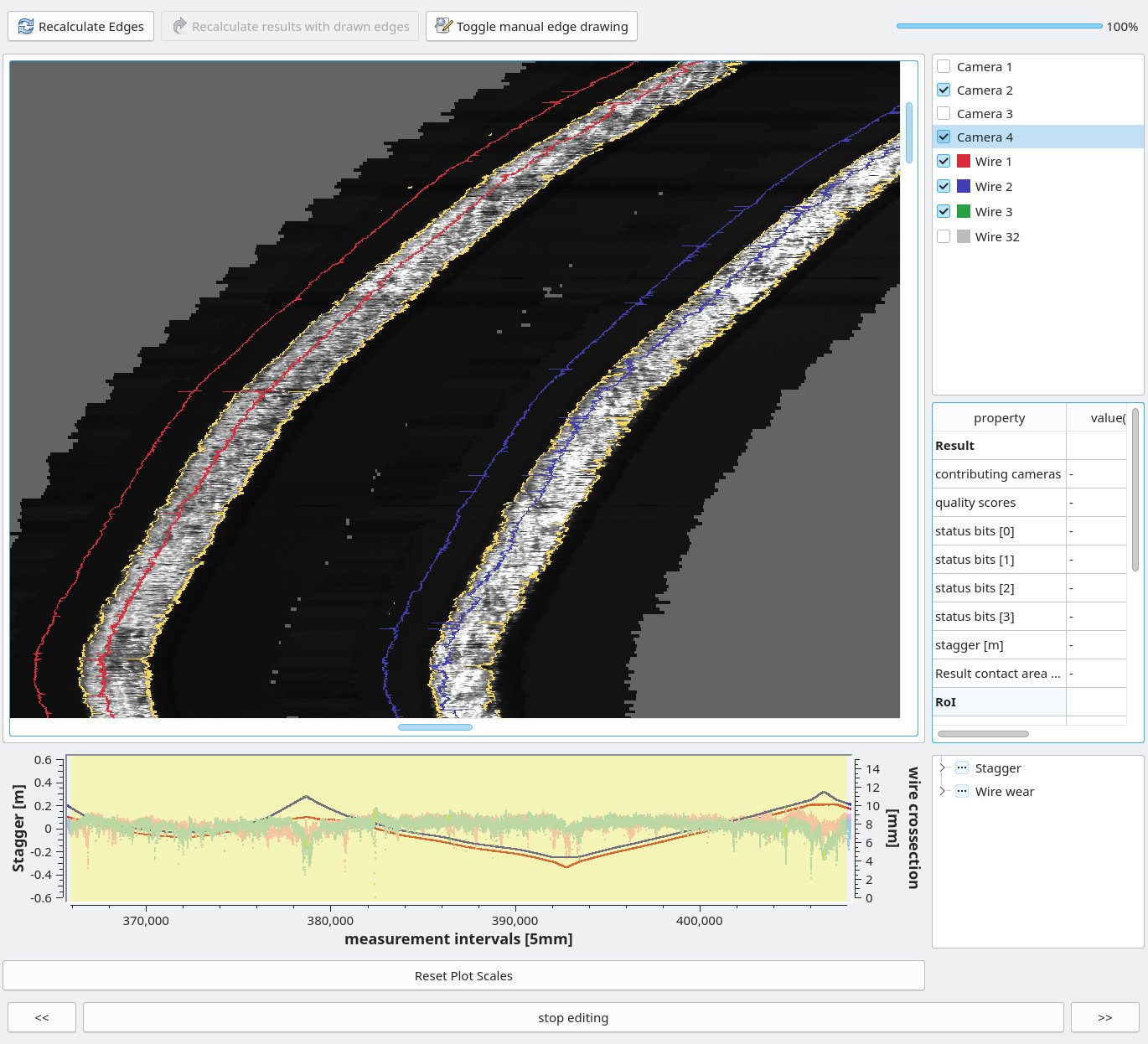
Most trains today run on electricity and are supplied with power by overhead line systems. While the train is in motion, the so-called pantograph permanently slides against the overhead line, mostly made of copper, with a certain contact pressure. In the long run, the overhead contact line wears out, threatening to break – with potentially fatal consequences. Therefore, overhead contact wires need to be replaced as soon as they have fallen below a specified thickness. Railway companies therefore check the contact wire thickness at regular intervals – if possible quickly and efficiently in regular operation.
Wire Wear Monitoring System WWS
The contact Wire Wear Monitoring System WWS, developed by Fraunhofer IPM, measures the degree of wear of up to ten contact wires – simultaneously and without touching them. The residual thickness of contact wires with a round profile is calculated from the width of their sliding surface. The camera-based Wire Wear Monitoring System WWS picks up the sliding mirror and at a speed of 100 km/h derives an indication of the degree of wear of the wires typically every 13 mm. We develop customer-specific solutions for contact wires with atypical cross-sections.
Due to its high measurement frequency and fast data processing, the Wire Wear Monitoring System WWS is suitable for speeds of up to 250 km/h. Thanks to an independent lighting unit, the system does not require daylight and is therefore also able to operate reliably at night, in tunnels or under bridges.
Keeping the entire overhead line in view
The Wire Wear Monitoring System WWS is also part of the multi-sensor system CIS (Contact Wire Inspection System) and its low-speed variant CIS-LS. These systems record contact wire wear and contact wire position simultaneously and, optionally, identify the position of poles.