Markerfreie Bauteil-Verfolgung im Produktionsprozess – Projekt »Track-4-Quality« geht an den Start
Funktion und Langlebigkeit teurer Baugruppen und fertiger Produkte hängen von der Qualität ihrer Einzelbauteile und Halbzeuge ab – auch wenn diese nur wenige Cent kosten. Im Rahmen des jetzt gestarteten Forschungsprojekts »Track-4-Quality« entwickelt Fraunhofer IPM gemeinsam mit Partnern aus Industrie und Forschung ein kostengünstiges, markierungsfreies Rückverfolgungsverfahren speziell für Massenbauteile.
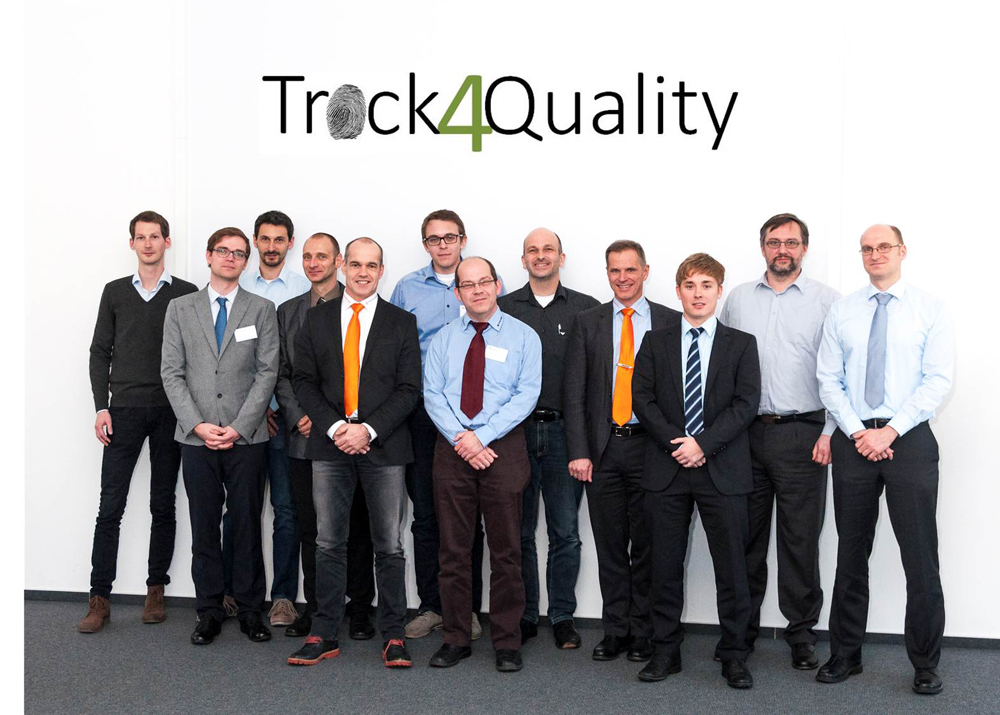
Am 10. Dezember 2015 startete das Forschungsprojekt »Track-4-Quality« ganz offiziell mit einem Kick-Off-Treffen am Fraunhofer IPM. Ziel des Projekts ist ein markierungsfreies Rückverfolgungsverfahren, das auch kleine Bauteile anhand ihrer Oberflächenstruktur erkennt und so eine Rückverfolgbarkeit durch komplexe industrielle Fertigungsprozesse erlaubt. Die lückenlose Rückverfolgung über den gesamten Produktionsprozess ist eine wichtige Voraussetzung für nachhaltige Qualitätssicherung und Prozessverbesserung in der industriellen Produktion.
Bauteile und Halbzeuge werden bereits heute immer häufiger markiert, um sie in der Produktion und auch später eindeutig identifizieren zu können. Bei vielen Massenbauteilen ist jedoch eine Markierung aufgrund ihrer Größe, Funktion oder aber aus hygienischen Gründen oftmals nicht praktikabel oder schlicht zu teuer. Im Rahmen von »Track-4-Quality« setzen die beteiligten Partner daher auf eine markerfreie Identifikation, die Bauteile allein anhand ihrer Oberflächenstruktur erkennen kann. Unterm Mikroskop zeigen technische Oberflächen zufällige Materialstrukturen, die für jedes Bauteil individuell sind – vergleichbar einem Fingerabdruck. Um diese Strukturen bei hohen Taktraten im Produktionsprozess zu erkennen, entwickeln die Wissenschaftler am Fraunhofer IPM ein kamerabasiertes System, das aus einer Bildaufnahme in Echtzeit eine digitale Bauteil-Signatur errechnet, die die Komponente eindeutig identifiziert. Das Verfahren soll unter anderem in der Gussfertigung von Metall- und Kunststoffteilen erprobt werden.
Bei ihrem Kick-off-Treffen betonten die Projektpartner die Chancen und weitreichenden Konsequenzen des Konzepts im Sinne der Industrie 4.0. »Rückverfolgung bis zur letzten Schraube – darin liegt ein ungeheures Potenzial«, erklärt Dr. Daniel Carl, Projektkoordinator am Fraunhofer IPM. »Wenn es uns gelingt, jedes Bauteil kostengünstig bis in ganz frühe Produktionsstadien zurückzuverfolgen, können wir systematische Fehler aufspüren und so Prozesse verbessern. Am Ende reichen die Konsequenzen einer lückenlosen Rückverfolgung bis hin zu Fragen der Haftung.«
Durch das Bundesministerium für Bildung und Forschung (BMBF) im Rahmen der Ausschreibung »Sensorbasierte Elektroniksysteme für Anwendungen für Industrie 4.0 (SElekt I4.0)« gefördertes Verbundprojekt.
Hintergrund: Das Projekt »Track-4-Quality«
Das Projekt »Track-4-Quality« ist auf zweieinhalb Jahre angelegt und umfasst ein Fördervolumen von 1,73 Millionen Euro. Drei Viertel dieser Summe stellt das Bundesministerium für Bildung und Forschung im Rahmen des Förderschwerpunkts »Sensorbasierte Elektroniksysteme für Anwendungen für Industrie 4.0« zur Verfügung. Projektpartner sind neben Fraunhofer IPM (Koordination) Hahn-Schickard Stuttgart sowie die Industriefirmen Otto Klumpp GmbH, Balingen, Seuffer GmbH & Co KG, Calw, Georg Fischer Automobilguss GmbH, Singen, und Sensopart Industriesensorik, Gottenheim (assoziiert).