Forschungsprojekt AKS-Bipolar startet
Qualitätssicherung für die Brennstoffzellen-Produktion
Eine zentrale Komponente von Brennstoffzellen sind sogenannte Bipolar-Platten, die bislang in der Regel aus Graphit hergestellt werden. Metallische Bipolar-Platten sind im Hinblick auf Effizienz und Wirtschaftlichkeit deutlich überlegen. Bei der Herstellung kommt es durch die Materialumformung jedoch oftmals zu Qualitätsproblemen. Im Forschungsprojekt AKS-Bipolar entwickelt Fraunhofer IPM gemeinsam mit der Universität Stuttgart und den Industriepartnern ThyssenKrupp und Chemische Werke Kluthe einen digital-holographischen Sensor zur vollständigen Qualitätsprüfung metallischer Bipolarplatten in der Produktionslinie.
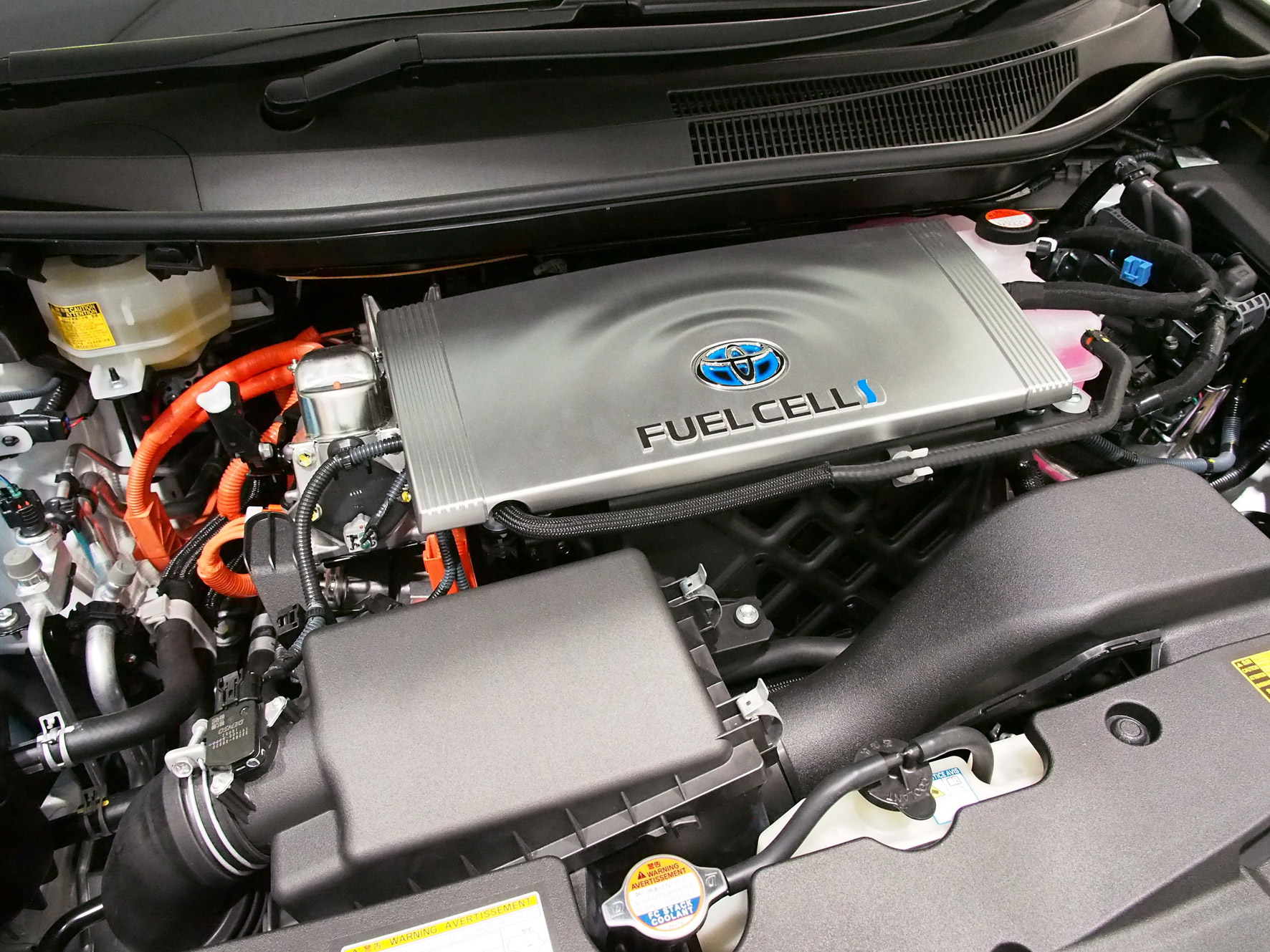
Leistungsstarke Brennstoffzellensysteme sind eine wichtige Voraussetzung, um Wasserstoff zur klimafreundlichen Erzeugung von elektrischer Energie zu nutzen. Brennstoffzellsysteme bestehen aus zahlreichen stapelartig angeordneten Membran-Elektroden-Einheiten (MEA), in denen die Umwandlung von chemischer zu elektrischer Energie stattfindet. Bipolarplatten (BPP) liegen zwischen diesen Einheiten und sorgen dafür, dass Reaktionsgase zu- und das entstehende Wasser abgeleitet werden. In modernen Brennstoffzellenstacks sind je nach Typ und Größe 300 bis 600 BPP mit einer Größe von standardmäßig etwa 400 mal 200 Millimeter verbaut.
Während graphitische BPP in einem aufwändigen zerspanenden Verfahren hergestellt werden, werden metallische BPP durch Kaltumformung gefertigt. Dies ist nicht nur kostengünstiger, sondern ermöglicht zudem einen deutlich schnelleren Produktionstakt. Ein weiterer Vorteil metallischer BPP: Der Werkstoff ist weniger spröde und lässt sich in geringeren Dicken verarbeiten, was eine Voraussetzung für den Einsatz beispielsweise im Automobil ist. Metallische BPP werden aus Feinstblechen bzw. Metallfolien mit Dicken unter 0,1mm gefertigt. Bei der Umformung kommt es jedoch häufig zu Oberflächendefekten oder Maßabweichungen, die die Montage der Zellenstapel erschweren und die Funktion der Brennstoffzelle beeinträchtigen. Bisher werden die meisten Fehler in der Produktion nicht zuverlässig erkannt, weshalb die Qualitätsprüfung nachgelagert in kosten- und zeitintensiven Stichprobentests erfolgt.
3D-Sensor soll Mikrodefekte im Umformprozess erkennen
Im Projekt AKS-Bipolar (Aktive Prozesskontrolle bei der Serienfertigung hochpräzise geprägter Bipolarplatten) entwickeln die Forschungspartner ein Prüfsystem zur aktiven Prozesskontrolle und Qualitätssicherung, das metallische BPP im Umformungsprozess mikrometergenau und vollständig prüft. Dazu werden Simulationsdaten mit den Messdaten eines digital-holographischen 3D-Sensors abgeglichen. Ziel ist eine umfassende Simulations-Toolchain: Diese beinhaltet einen Digitalen Zwilling des Umformprozesses, anhand dessen wiederkehrende Fertigungsprobleme numerisch erfasst und systematisch beseitigt werden können.
Der inline-fähige 3D-Sensor, der am Fraunhofer IPM entwickelt wird, generiert hochgenaue Messdaten in Echtzeit. Die Simulationsdaten stellt das Team des Instituts für Umformtechnik (IFU) der Universität Stuttgart bereit. Das System wird als Demonstrator aufgebaut und von den assoziierten Industriepartnern ThyssenKrupp System Engineering und Chemische Werke Kluthe im Industrieumfeld getestet. Es soll in Zukunft helfen, kritische Prozessparameter zu identifizieren, um Produktionsfehler gezielt zu beheben. So lassen sich Ausschuss minimieren, Simulationsmethoden weiterentwickeln und letztendlich der Produktionsprozess bei der Herstellung metallischer BPP optimieren.
Weitere Informationen
Das Projekt AKS-Bipolar (Aktive Prozesskontrolle bei der Serienfertigung hochpräzise geprägter Bipolarplatten) wird im Rahmen der »trilateralen Projekte« von der Deutschen Forschungsgemeinschaft (DFG) und der Fraunhofer-Gesellschaft gefördert.
Projektpartner
- Institut für Umformtechnik IFU, Universität Stuttgart
- Fraunhofer-Institut für Physikalische Messtechnik IPM
- Thyssenkrupp System Engineering GmbH (Anwendungspartner)
- Chemische Werke Kluthe GmbH (Anwendungspartner)
Projektlaufzeit
Das Projekt startete im Oktober 2021 und ist auf drei Jahre angelegt.