Brennstoffzellenproduktion
Digital-holographischer 3D-Sensor sichert Qualität metallischer Bipolarplatten
Ein digital-holographischer Sensor prüft die Qualität metallischer Bipolarplatten für Brennstoffzellen mit einer Genauigkeit im Bereich weniger Mikrometer und ermöglicht erstmals eine vollständige Inline-Qualitätskontrolle. Die Sensordaten sind darüber hinaus Basis für einen digitalen Zwilling des gesamten Umformprozesses. Dieser soll helfen, Ursachen für wiederkehrende Fehler zu verstehen und den Fertigungsprozess zu optimieren.
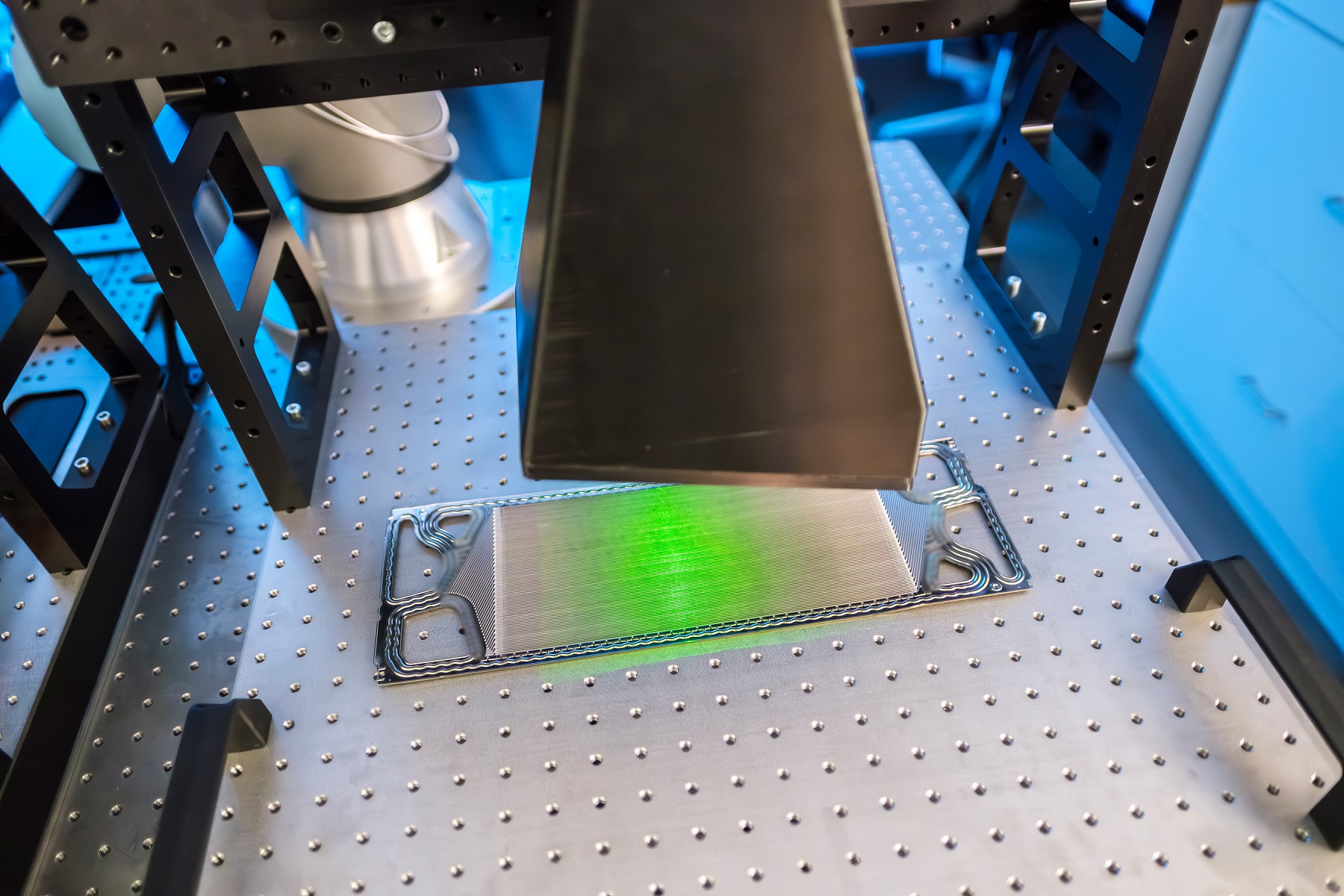
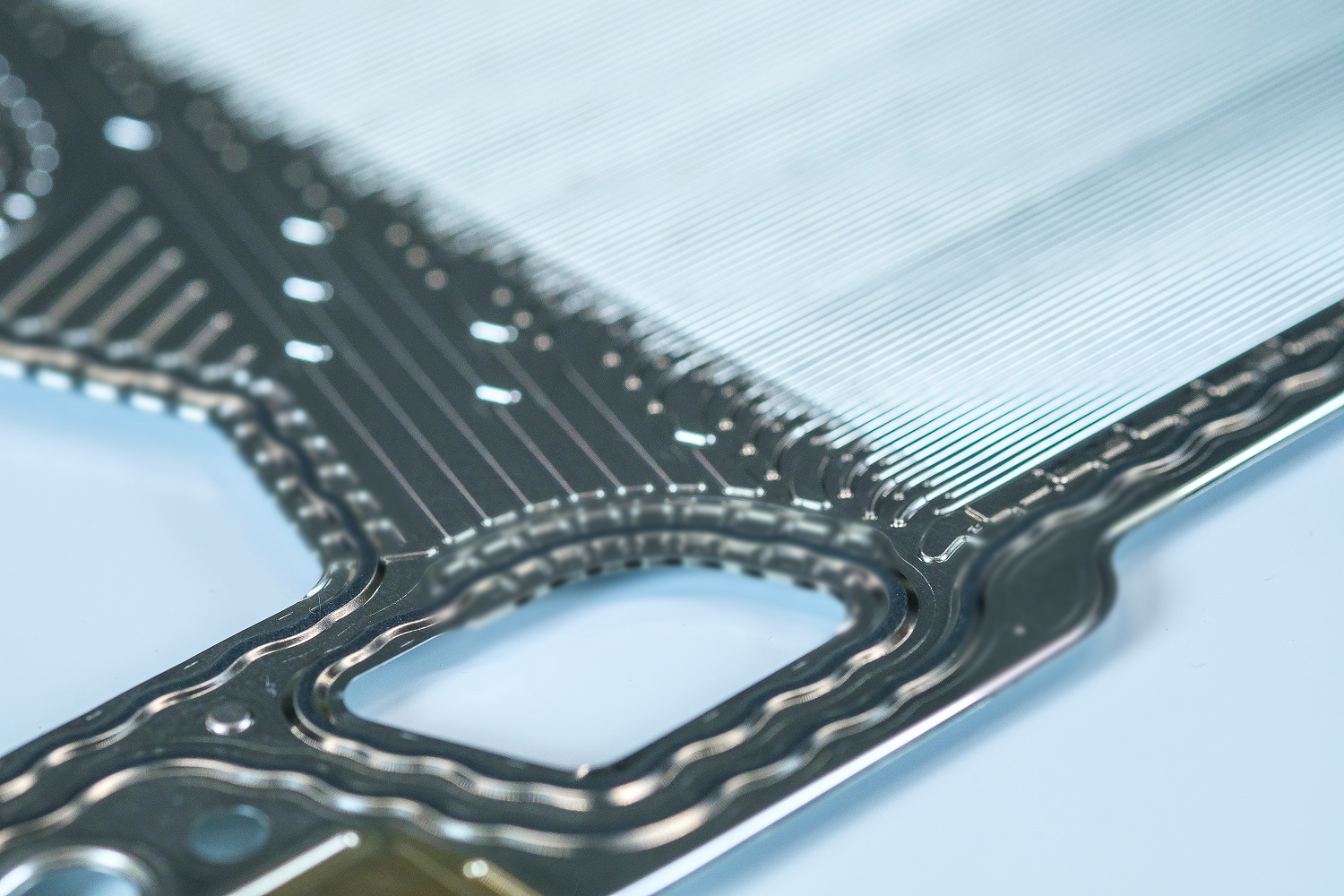
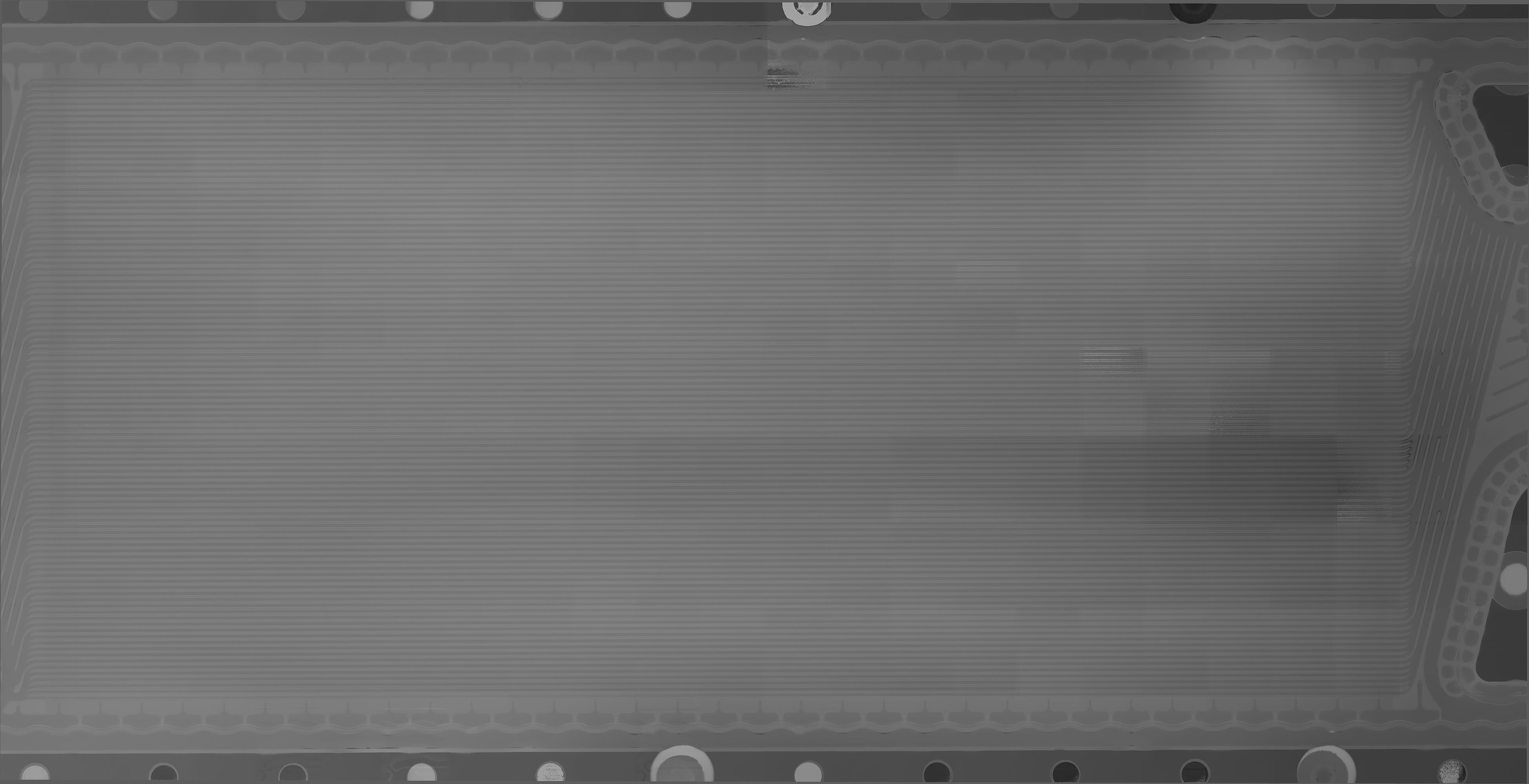
Bipolarplatten sind Schlüsselkomponenten in Brennstoffzellen. Bis zu sechshundert dieser Bauteile werden in einer Brennstoffzelle zu Stapeln geschichtet; sie sorgen u.a. für die elektrische Verbindung sowie die Verteilung und Ableitung von Reaktionsgasen und Wasser. Metallische Bipolarplatten werden aus teilweise weniger als ein Zehntel Millimeter feinen Metallfolien Metallfolien beidseitig geprägt. Leicht schwankende Prozessparameter bei der Umformung führen zu typischen Fehlern wie z. B. Reißern, Falten oder Springbeul-Effekten, die die Funktion und Langlebigkeit der Brennstoffzelle beeinträchtigen. Solche Fehler konnten bisher nur durch eine nachgelagerte Qualitätskontrolle stichprobenartig erkannt werden. Im Rahmen eines Kooperationsprojekts der Fraunhofer-Gesellschaft und der Deutschen Forschungsgemeinschaft hat Fraunhofer IPM gemeinsam mit der Universität Stuttgart sowie den Industriepartnern thyssenkrupp Automation Engineering und Chemische Werke Kluthe Sensortechnik und Simulationsverfahren entwickelt, die die Grundlage bilden für eine aktive Prozesskontrolle und Prozessoptimierung bei der Serienfertigung umgeformter Bipolarplatten.
Vollflächige Vermessung großer Flächen mit Mikrometergenauigkeit
Ein am Fraunhofer IPM entwickelter digital-holographischer 3D-Sensor nimmt hochgenaue 3D-Daten der Bauteiloberfläche auf und stellt sie in Echtzeit für die Prozesskontrolle zur Verfügung. Um Bipolarplatten unterschiedlicher Größe zu vermessen, setzen die Forschenden auf ein skalierbares System, das je nach Bauteilgröße um weitere Messköpfe erweitert werden kann. Ein solcher aus mehreren Sensorköpfen bestehender »Matrixsensor« nimmt das gesamte Flussfeld von Bipolarplatten mit einer Größe von bis zu 400 mm × 150 mm in einem einzigen Messdurchgang auf – in weniger als einer Sekunde und ohne Verfahren des Sensors. Ein Stitching-Algorithmus setzt die Messdaten der einzelnen Messfelder zu einem Gesamtbild zusammen. Die hochaufgelösten Messbilder zeigen Umformfehler ab einer Größe von wenigen Mikrometern. Das System wird aktuell in einer seriennahen Umgebung am Institut für Umformtechnik IFU der Universität Stuttgart getestet.
Aus Fehlern lernen: Wertvolle Daten für die Prozessoptimierung
Die vom digital-holographischen Sensor erfassten Messdaten sollen nicht nur Gut- und Schlechtteile unterscheiden, sondern den Produktionsprozess nachhaltig verbessern. Dazu wurde an der Universität Stuttgart eine umfassende Simulations-Toolchain des Umformprozesses entwickelt, in die die 3D-Messdaten einfließen. So sollen wiederkehrende Fehlerbilder systematisch erfasst und analysiert werden, sodass Prozessparameter angepasst werden können.