Stahl-Innovationspreis für Echtzeit-Laserschweißregelung
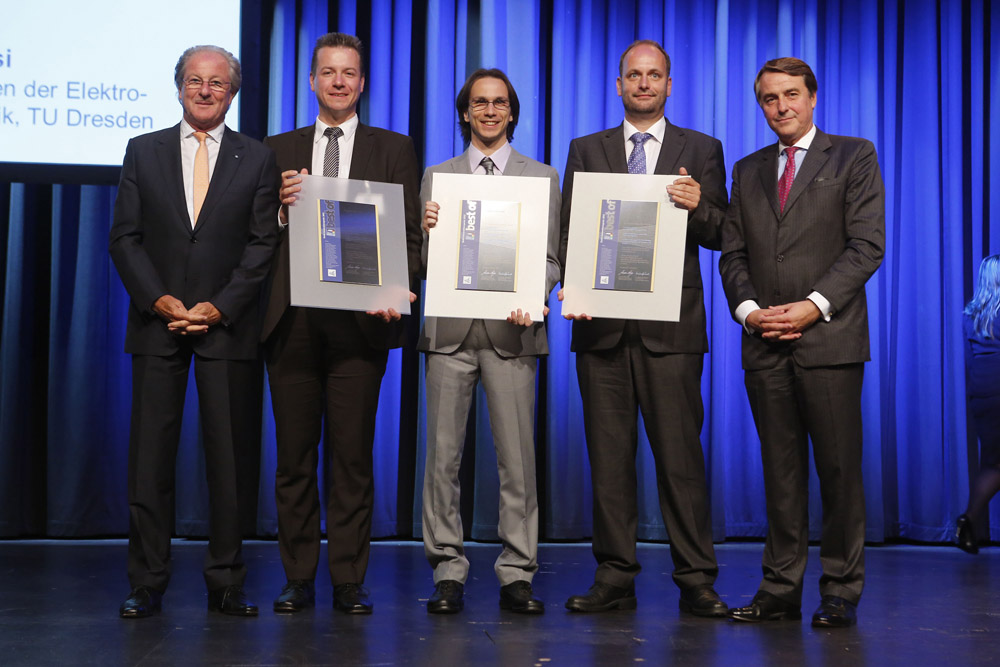
Das Fraunhofer-Institut für Physikalische Messtechnik IPM ist für die Entwicklung eines Messsystems zur Echtzeit-Laserschweißregelung mit dem Stahl-Innovationspreis ausgezeichnet worden. Das Institut belegte den dritten Platz in der Kategorie »Forschung und Entwicklung« gemeinsam mit den Entwicklungspartnern vom Institut für Strahlwerkzeuge der Universität Stuttgart und dem Institut für Grundlagen der Elektrotechnik und Elektronik der Technischen Universität Dresden. Die insgesamt 13 Preisträger nahmen die Auszeichnung in Düsseldorf aus den Händen des Schirmherrn Prof. Dr.-Ing. Wolfgang Reitzle, Vorsitzender der Linde AG, und des Vorsitzenden des Stahl-Informations-Zentrums, Dr. Jost A. Massenberg, entgegen.
Laserstrahlschweißen hat sich als schnelles und flexibles Fügeverfahren in vielen Anwendungsbereichen bewährt. Im automobilen Karosseriebau ermöglicht es nicht nur die effiziente Herstellung von Baugruppen, sondern trägt bei entsprechender Konstruktion auch zum Leichtbau und zu verbesserten Struktureigenschaften bei. Bei dem in der Karosseriefertigung üblichen Tiefschweißen erschweren die komplexen und hochdynamischen physikalischen Vorgänge in der Schmelzzone bislang eine präzise Regelung des Fügeprozesses. Wichtiges Qualitätsmerkmal ist das bei vollständigem Aufschmelzen des Materials entstehende Durchschweißloch. Es stellt sicher, dass der gesamte Querschnitt der Bleche genutzt wird. Übliche Prozessüberwachungssysteme auf Basis von Photodioden erkennen lediglich die Intensität der Strahlung, nicht aber ihre örtliche Verteilung. Bildgebende Sensoren bzw. Kameras erlauben die Erfassung von örtlicher Strahlungsverteilung und Durchschweißloch. Eine Online-Regelung des Prozesses ist aber aufgrund der geringen Bildraten von 1 bis 2 kHz nicht möglich.
Neue Bildverarbeitungstechnologie und spezielle Regelstrategie
Das am Fraunhofer IPM mit entwickelte System zur Laser-Schweißregelung nutzt eine neue Art der Bildverarbeitungstechnologie, bei der in jedes der insgesamt 25.000 Pixel des Aufnahmechips der Kamera ein eigener Mikroprozessor integriert ist. Die Mikroprozessoren sind über so genannte zellulare neuronale Netzwerke miteinander verknüpft und verarbeiten die gewonnenen Bilddaten parallel. Mit Bildraten von 14 kHz ist eine statistische Analyse des Durchschweißlochs innerhalb der Reaktionszeit des Schweißprozesses möglich. Durch eine speziell entwickelte Regelstrategie kann die Laserleistung bei Prozessschwankungen wie verschmutzter Laseroptik, Vorschubschwankungen oder Veränderungen der Fokuslage erstmals in Echtzeit angepasst werden. Auf diese Weise wird immer exakt so viel Laserleistung abgerufen, dass der gesamte Querschnitt der Fügeteile für die maximale Festigkeit genutzt wird. Dies verbessert die Qualität der Schweißverbindung, weil Leistungsüberschüsse und somit Schweißrauch und Spritzer vermieden werden. Der Energieeinsatz kann dadurch um etwa fünf Prozent verringert werden.
Mit dem neuen System ist auch das »geregelte Einschweißen« bei Überlappverbindungen möglich: Hierbei wird das am Spalt zwischen Oberblech und Unterblech entstehende Durchschweißloch genutzt, um die Einschweißtiefe im Unterblech zu regeln. Es wird gerade so weit in das Unterblech geschweißt, dass dessen Unterseite nicht verletzt wird und sich später ohne optische Beeinträchtigung lackieren lässt. In diesem Fall sind bei gleicher Nahtfestigkeit sogar Energieeinsparungen bis zu 30 Prozent möglich. Beim geregelten Einschweißen in verzinkte Stahlbleche bleibt zudem die Korrosionsschutzwirkung an der Unterseite vollständig erhalten, da hier keinerlei Zink verdampft. Damit verbessert die Echtzeitregelung den Einsatz der Laserschweißtechnik auch im Außenhautbereich von Karosserien.