Track & Trace via Fingerprint
Marker-free component tracking achieves 99.95 percent identification rate in production
To improve industrial production processes, it is important to be able to assign production data to individual components. The Track & Trace Fingerprint technology developed by Fraunhofer IPM makes it possible to trace components without marking. The concept also proves to be extremely reliable in production environments, as has now been demonstrated in a pilot production facility at research partner Bosch.
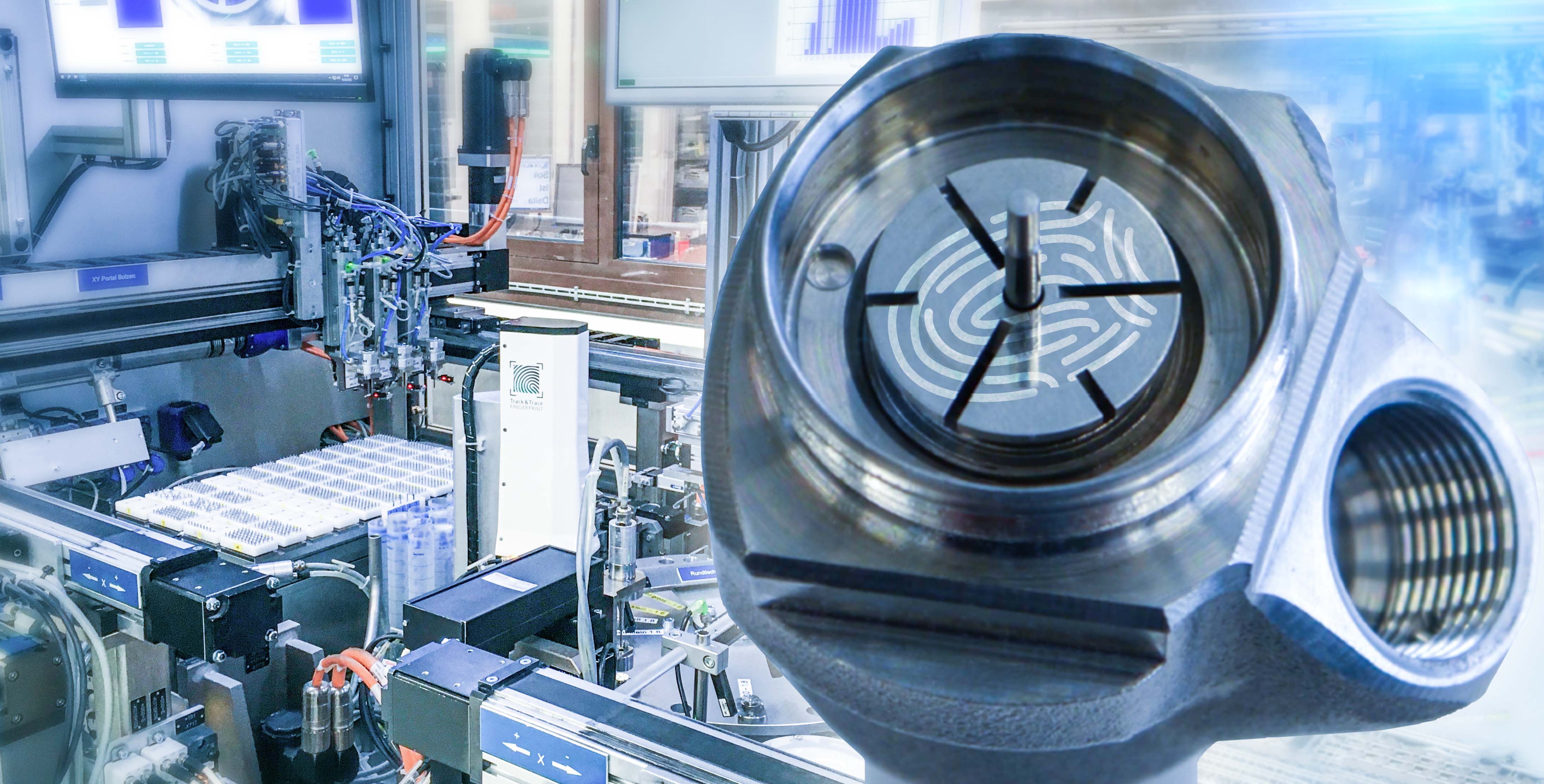
Track & Trace Fingerprint uses the individual microstructure of component surfaces as a „fingerprint“ for identification. This has several advantages: Applying a machine-readable marking, such as a data matrix code (DMC), is no longer necessary. In some cases, where applying a marker is not practicable due to the component‘s size, geometry or functional surfaces, Track & Trace Fingerprint makes component tracing possible for the first time. This holds true for a so-called anchor component which is produced in large quantities at a production facility of automotive supplier Robert Bosch GmbH in Bamberg. These small, round shaped armatures are installed in every Common Rail Injector. Together with Bosch, Fraunhofer IPM has succeeded in reliably identifying almost 100 percent of the components in the production process in 30,000 random samples each made up of 100,000 anchors.
High demands on robustness and speed
In the Track & Trace Fingerprint process, a camera system captures defined areas of the component surface in high resolution. From the image data with their specific structural patterns and their position in relation to each other, a numerical code, the fingerprint, is calculated and assigned to an ID. Both, fingerprint and ID are stored in a database. This whole process is repeated for later component identification: If the fingerprints match, the ID is returned to the user.
Various challenges arise when using the technology under real production conditions:
Extremely fast production cycles require extremely fast data processing. Different light conditions during image acquisition and identification as well as positioning inaccuracies must be compensated for by software. Finally, installation space and working distance in the existing plant are limited.
The armatures‘ easily accessible top pole surface was chosen as fingerprint area. However, the polished, reflective surface is a challenge for the optical system. Due to the sixfold symmetry of the pole surface, there are six possible rotation angles. Therefore, six fingerprints were generated and matched for each armature within a matter of a second. The pilot test has shown that with the Track & Trace Fingerprint technology, enables a 1:1 allocation of process data even for mass-produced components.